Overview: What is Penetrant Testing?
Working principle of Penetrant Testing: A dye is applied onto the surface of the inspected part, for example by spraying. After a defined time, the liquid is removed again from the surface, while some amount of it remains within cracks and similar defects. To make these defects visible, a developer is applied and the inspection is conducted under special lighting conditions, usually ultraviolet. Afterwards, all dye remnants are comletely cleaned off.
Variations:
- Dye penetrant inspection
- Flourescent penetrant inspection
Use cases: detection of surface defects like cracks or porosity; possible at high speed and low cost
Materials: non-porous materials like plastic or metal
Testia’s qualifications: EN 4179 & ISO 9712 – see the full list of Testia’s qualifications on our certification page
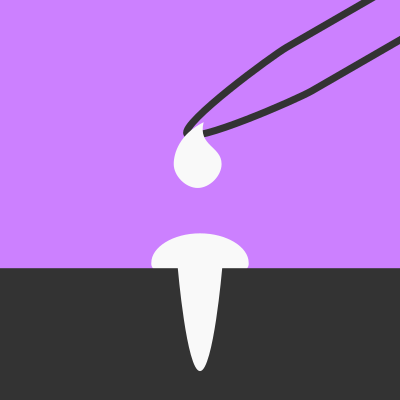
Testia's Penetrant Testing Services
We offer penetrant inspection services for manufacturing in various industry sectors and in-service inspection (Part-145) for aerospace. We can perform both visible penetrant inspections and fluorescent penetrant inspections, either mobile on-site or in our PT labs for serial inspections. Furthermore, Testia offers Level 3 consultancy as well as PT training courses and bespoke PT inspection systems.
Typical use cases for this method include:
- Pipes and containers
- Turbine parts
- Various aircraft parts
- Welds (e.g. on ships and pipes)
- Valves
Testia's Penetrant Testing Products
Penetrant Testing Systems
Performance and flexibility with Testia’s Penetrant Inspection (PT) systems for production parts and MRO
Reference Blocks
Assure precise inspection measurements for any aerospace NDT device – thanks to our comprehensive catalog of reference blocks Reference blocks