3D-Metrologie ermöglicht es, verbesserte CAD-Daten aus Scans von alten oder verformten Teilen und Fertigungsmitteln zu reverse-engineeren.
(Dieser Artikel erschien zuerst auf English im Magazin Aerospace Testing International, showcase 2025 issue)
In der Produktion werden sich Fertigungsmittel und Werkzeuge (Jigs and Tools) sowie andere Teile früher oder später abnutzen oder sogar verformen. Damit gehen substanzielle Risiken für die Fertigung einher: Defekte Geräte könnten den Dienst verweigern oder zu Bruch gehen und verformte Fertigungsmittel bieten keine gleichbleibende Form und Qualität der gefertigten Teile mehr.
Um diese Probleme zu vermeiden, sind regelmäßige Prüfungen unerlässlich. Doch welche Möglichkeiten bestehen überhaupt noch, wenn die Defekte die Toleranzgrenzen überschritten haben? Ein Fertigungsmittel zu reparieren oder durch ein neues zu ersetzen, ist meist nur anhand technischer Zeichnungen möglich – und diese sind oft nicht mehr aufzufinden. Je älter Jigs und Tools sind, umso weniger wahrscheinlich ist es, dass noch Zeichnungen existieren – geschweige denn CAD-Daten.
Yes, we (s)can!
Die Lösung ist erfreulich einfach: 3D-Scans. Genauer gesagt ein reverse-engineertes 3D-Modell, das auf einem Metrologie-Scan des Orginalteils basiert. Das Scanning selbst ist ein übliches Verfahren, doch das Metrologie-Team von Testia ist spezialisiert auf das anschließende Reverse-Engineering. Hier kommt der eigentliche Mehrwert zum Vorschein und jeder einzelne Arbeitsschritt bietet bereits praktische Vorteile für die Kundschaft.
Ein Projekt beginnt direkt vor Ort bei den Auftraggebern. Der Scanner und der dazugehörige Rechner eignen sich bestens für den mobilen Einsatz. So kann unser Scanning-Ingenieur den Aufbau zum Beispiel direkt in der Fertigungshalle aufstellen. Obwohl der Aufbau platzsparend ist, können damit nicht nur kleine, sondern auch sehr große Strukturen mit hoher Genauigkeit gescannt werden (+/-0.025 mm bei 1 m³ Messvolumen). Eine Projektor strahlt blaues Licht auf das zu scannende Teil und eine Stereokamera zeichnet das reflektierte Licht wieder auf. Diese Methode lässt sich für zahlreiche verschiedene Oberflächentypen und -ausmaße anwenden, indem mehrere Scanvorgänge kombiniert werden. Neben flachen Oberflächen lassen sich ebenfalls weit komplexere Bauteilgeometrien erfassen.
Dank der hohen Auflösung erhält der Scanning-Ingenieur ein Polygonnetz, das selbst kleinste Deformierungen und Oberflächendefekte anzeigt. Mit dieser digitalen Darstellung der Messdaten geht es weiter zum nächsten Schritt, der Analyse. Sie kann entweder direkt am Standort durchgeführt werden oder an einem separaten Arbeitsplatz.
Einen Schritt voraus
Bis zu diesem Punkt hat die Methode der 3D-Messtechnik bereits wertvolle Informationen bereitgestellt. Sowohl Scandaten als auch Evaluierungsberichte können in verschiedenen Formaten exportiert werden und liefern wichtige Daten über die Sturkturintegrität eines Bauteils. Allerdings kann das Testia-Team mit ein paar zusätzlichen Schritten noch weitaus mehr Vorteile herausholen. Als nächstes folgt der Soll-Ist-Vergleich, also ein Abgleich der gemessenen Daten mit dem eigentlich optimalen Zustand der unbeschadeten Teile bzw. Strukturen.
Wenn die entsprechenden Soll-Daten bereits verfügbar sind, so ist der Vergleich eine Sache von wenigen Klicks in der Software. Dieser schnelle Abgleich ist sogar für eine In-Line-Qualitätskontrolle in der seriellen Produktion geeignet. Die Software beinhaltet alles, was für die Qualitätsprüfung benötigt wird: Funktionen für den Import der Soll-Daten, automatisierte Suche nach Abweichungen in den Messdaten und den Export der Ergebnisse.
Sollten die Soll-Daten jedoch nicht vorliegen, können sie aus den Metrologie-Messdaten abgeleitet werden: Zurück bei Testia macht sich unser Experte für Reverse Engineering ans Werk – er nutzt die Punktwolke des Scans, um ein optimiertes 3D-Modell zu erstellen. Alle Ungänzen und Schäden am Orginalteil werden im Scan abgebilded, wie bei einem ditigalen Zwilling. Doch nun wird das 3D-Modell digital wieder in Bestform gebracht. Zu diesem Zweck nutzt der Reverse-Engineering-Experte reguläre Geometrien: Wenn beispielsweise das Orginalteil quaderförmig ist und ein paar Dellen aufweist, ersetzt er es im 3D-Modell durch einem optimalen Quader mit glatten Flächen. Komplexere Strukturen rekonstruiert er, indem er mehrere reguläre Geometrien und Freiformen kombiniert. Das Ergebnis als CAD-Datei zeigt nicht nur die ideale Form ohne Defekte, sondern hat außerdem eine optimierte Dateigröße. Denn reguläre Geometrien können weitaus effizienter gespeichert werden als ein hochaufgelöstes Polygonnetz, das an diesem Ende des Gesamtprozesses nicht mehr benötigt wird.
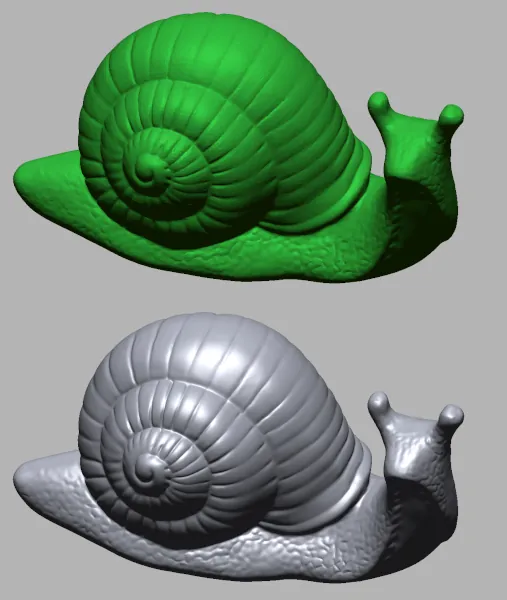
Messen, analysieren, verbessern
Mit der reverse-engineerten CAD-Datei können Sie nun ein Ersatzteil fertigen lassen, um das defekte zu ersetzten. Es ist sogar noch mehr möglich: Anstatt eine exakte Nachbildung des Orginals zu fertigen, kann Testia auch maßgefertigte Anpassungen in das neue 3D-Modell integrieren. Ihr Produktionsteam könnte beispielsweise bessere Griffpositionen an einem Werkzeug vorschlagen oder eine einst überdimensionierte Halterung kann durch eine geeignete schmalere Struktur ersetzt werden, die sich besser in die Produktionsstraße einfügt. Was zuvor undenkbar war, kann nun dank Testias Reverse-Engineering-Team verwirklicht werden.
Das Schöne an dem gesamten Prozess ist, dass er Einfachheit und Komplexität verknüpft: exakte Messungen komplexer Strukturen einerseit und einfach umzusetzende Verbesserungen andererseits. Das Resultat ist ein optimiertes 3D-Modell als zuverlässigste Grundlage, um Ersatzteile für abgenutzte Strukturen herzustellen. Albtraumszenarien über Produktionsausfälle durch kaputte Fertigungsmittel gehören dann der Vergangenheit an.
Erfahren Sie mehre über Testias 3D-Messtechnik und Reverse Engineering oder kontaktieren sie direkt unser Team für 3D-Metrologie.