Overview: What is Infrared Thermography Testing?
Working principle of infrared thermography testing: The tested part is stimulated, e.g. with ultrasonic bursts or halogen lights. An infrared camera captures the thermal response of the part as a result of the stimulation. This generates a thermal image that indicates defects and other properties of the part’s material.
Variations:
- Passive
- Active/Lock-in:
- Optical excitation (Halogen-, Ultrasonic-, Laser-Thermography etc.)
- mechanical excitation
- electromagnetical excitation
Use cases: sub-surface delamination, cracks detection; detection of material discontinuities (thickness differences), localisation of repairs, repaints or hidden parts; localisation of water inclusions
Materials: mainly carbon fiber and glass fiber; but ultrasonic burst thermography does also work with metals
Testia’s qualifications and certifications: EN 4179 – see the full list of Testia’s qualifications on our certification page
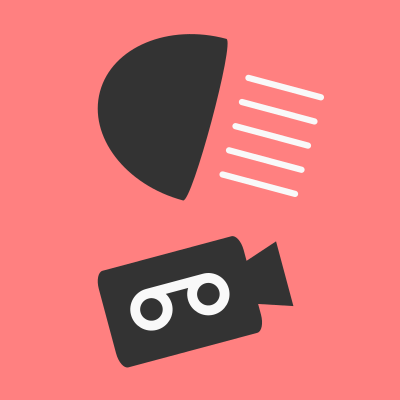
Testia's Thermography Inspection Services
We offer thermography inspection services for manufacturing in various industry sectors and in-service inspection (Part-145) for aerospace, Level 3 consultancy as well as TT/IRT training courses.
Typical use cases for this method include:
- thermal stress
- water ingress
- impacts
- delamination
- disbonding
Testia's Thermography Testing Products
IRT Inspection Systems
Automated thermography installation
Gecko
Direct, quick and reliable characterization of defects on vertical honeycomb repaired structures for assuring structural safety
Reference Blocks
Assure precise inspection measurements for any aerospace NDT device – thanks to our comprehensive catalog of reference blocks Reference blocks (also: reference standards, calibration blocks) are highly characterized, standardized and